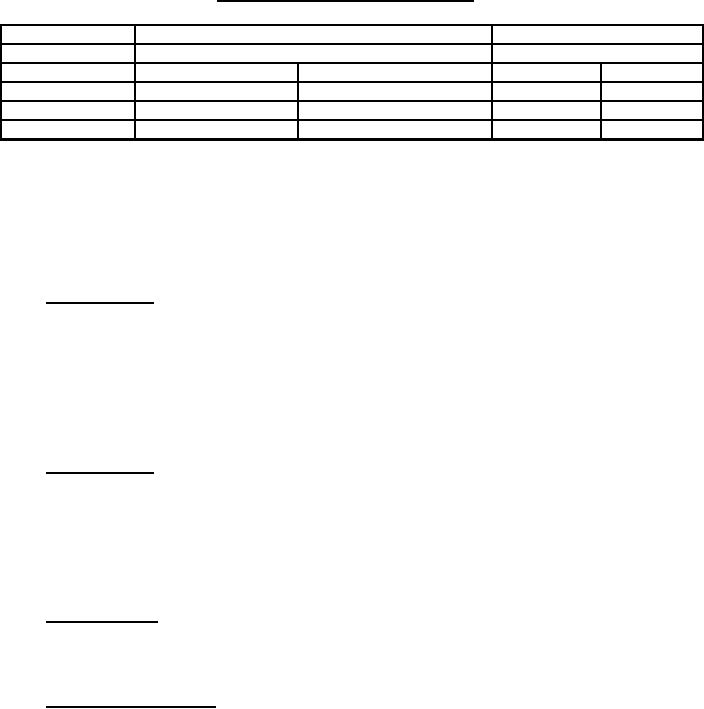
MIL-DTL-18295F
TABLE III. Chemical composition ladle analysis 2/ - Continued.
Mooring chain assembly components 3/
Swivel shackle pins only 3/
Percent
Percent
Element
Minimum
Maximum
Minimum
Maximum
Vanadium 1/
0.100
Aluminum 1/
0.065
Molybdenum 1/
0.080
0.20
0.300
Notes:
1/
Not less than one of these grain refining elements shall be used in enough quantity to ensure a fine grain
structure for chain and accessories.
2/
Table III does not include pear links, plate sinker shackles, split keys, lead plugs, or tapered pins. Chemical
composition for pear links is to be determined by the manufacturer to meet requirements of table I and
submitted with test reports (see 3.4.2).
3/
Conforming to SAE J404, class 1330 and 4330.
3.4.3 Heat treatment. All welding shall be completed prior to heat treatment. All inspection or
testing of the finished component shall take place after heat treatment. Components shall be
normalized above the transformation temperature or quenched and tempered, as required, to
produce a uniform fine grain structure which obtains mechanical properties to meet specifications.
Welded components shall not be quenched. All heat treating equipment shall be automatically
controlled and regularly checked. Temperature time charts shall be kept and be a part of the CoC
(see 4.2).
3.4.4 Microstructure. The grain size of each component shall be uniform throughout the cross
section of the finished component. Grains shall be equal to or finer than ASTM E 112 No. 6 as
determined by using the comparison method at 100 percent magnification. Randomly dispersed
grains as large as ASTM E 112 No. 4 are permissible. The components shall be heat treated to
refine the grain size and to minimize the presence of Widmanstatten structure in the finished
products (see 4.6.10).
3.4.5 Macrostructure. Each finished component shall be free from harmful defects such as
seams, voids, flakes, shuts, cracks, porosity, nonmetallic inclusions, segregations, and centerline
shrinkage (see 4.6.11).
3.4.6 Metal spray hard facing. The contact bearing surfaces between swivel sections shall be
hard faced by the metal spraying process. All surfaces to be faced shall be thoroughly prepared by
removal of all foreign material and corrosion products. A coating of a self-fluxing metal powder
composed of chromium, boron, nickel, and silicon shall be sprayed onto the prepared surfaces so
as to produce a finished coating, after fusing, of not less than 20-mil (0.5 mm) thickness. The
sprayed coating shall be fused to the base metal in accordance with the procedures recommended
by the supplier of the hard facing materials. Care shall be exercised to prevent overheating during
the fusing process in order to prevent running or sagging of the coating. The sprayed part shall be
cooled slowly in accordance with recommendations of the metal spray supplier. The finished
coating shall be fine texture, uniform thickness, free of unatomized or unfused particles of metal,
and shall have a hardness of 56 to 61 on the Rockwell C scale and a surface roughness of
250 RMS maximum.
10
For Parts Inquires submit RFQ to Parts Hangar, Inc.
© Copyright 2015 Integrated Publishing, Inc.
A Service Disabled Veteran Owned Small Business